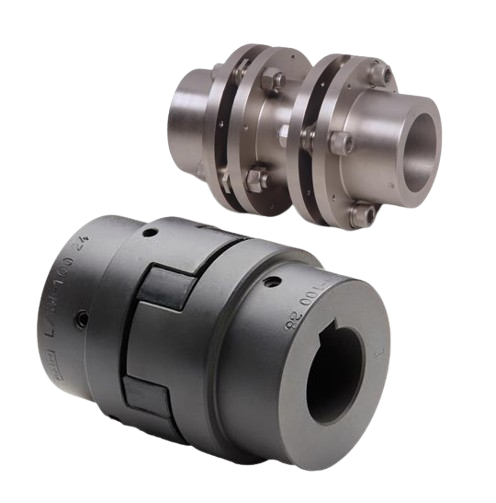
COUPLING
Pump and Motor Coupling. A pump and motor coupling is a mechanical device that connects a pump to a motor, allowing them to transmit power and motion while accommodating misalignment and vibration.
Types of Pump and Motor Couplings:
- Flexible Coupling: Allows for misalignment and vibration with a flexible design.
- Rigid Coupling: Connects two shafts with a solid, non-flexible design.
- Disc Coupling: High-torque capacity with a flexible disc design.
- Grid Coupling: High-torque capacity with a flexible grid design.
- Bellows Coupling: High-misalignment capacity with a flexible bellows design.
Pump and Motor Coupling Applications:
- Centrifugal Pumps: Connecting centrifugal pumps to motors.
- Positive Displacement Pumps: Connecting positive displacement pumps to motors.
- Submersible Pumps: Connecting submersible pumps to motors.
- Chemical Pumps: Connecting chemical pumps to motors.
- Wastewater Pumps: Connecting wastewater pumps to motors
Key Features:
- High-Torque Capacity: Transfers power and motion efficiently.
- Misalignment Accommodation: Allows for shaft misalignment and vibration.
- Corrosion-Resistant: Materials and coatings for harsh environments.
- Easy Installation: Simplified setup and alignment process.
- Low Maintenance: Minimal downtime and maintenance requirements.
Benefits:
- Improved Efficiency: Efficient power transmission and motion transfer.
- Reduced Vibration: Minimizes vibration transmission and noise.
- Increased Reliability: Robust design ensures consistent performance.
- Easy Maintenance: Simplified maintenance and repair process.
- Customization: Meets specific pump and motor application requirements.
Materials of Construction:
- Steel: Durable, heavy-duty construction.
- Stainless Steel: Corrosion-resistant, suitable for harsh environments.
- Aluminum: Lightweight, corrosion-resistant option.
- Coatings: Epoxy, ceramic, or specialized coatings for added protection.